2013年8月12日
独立行政法人理化学研究所
国立大学法人千葉大学
絶縁部分が4μmの次世代高温超伝導ワイヤを開発
-超伝導機器の小型化、高磁場化、低コスト化の実現に向けた一歩-
ポイント
- 絶縁部分の厚さを従来の10分の1以下の薄さで実現
- 次世代の主流を方向づける革新的な次世代高温超伝導ワイヤ
- NMRやMRIなどの超伝導機器をはるかにコンパクトに
要旨
理化学研究所(理研、野依良治理事長)と千葉大学(齋藤康学長)は、次世代の超伝導ワイヤ[1]として期待されるレアアース系の「次世代高温超伝導ワイヤ[1]」の絶縁部分の厚さを従来の10分の1となる4μmにすることに成功しました。これは、理研ライフサイエンス技術基盤研究センター(渡辺恭良センター長)構造・合成生物学部門 NMR施設の前田秀明施設長、柳澤吉紀基礎科学特別研究員、高橋雅人上級研究員らと、千葉大学大学院工学研究科の中込秀樹教授らとの共同研究グループによる成果です。
超伝導とは、極低温下で物質の電気抵抗がゼロとなり電流が流れ続ける現象です。この性質を持つ線材(超電導ワイヤ)で作られる超伝導コイルは、強い磁場を発生させる電磁石として、核磁気共鳴分光法(NMR)、磁気共鳴画像装置(MRI)、超伝導リニアモーターなどに応用されています。近年、従来の超電導ワイヤよりも性能が高いレアアース系の次世代高温超伝導ワイヤの開発が試みられており、実用化すれば超伝導機器のさらなる高磁場化、小型化を実現するキーテクノロジーになると期待されています。同ワイヤは幅が4~5mm、厚さが100~150μmの薄いテープ状です。超電導コイルとして利用するには短絡を防ぐためワイヤを絶縁材料で巻く必要がありますが、従来の絶縁方法では絶縁部分がワイヤと同程度の厚さになってしまい電流密度[2]が下がってしまいます。これが、超伝導コイルが大型化する原因でした。絶縁部分の厚さを1桁以上薄くできれば、電流密度が大きくなり超伝導コイルの大幅な小型化が可能なため極薄絶縁を実現する技術の開発が求められていました。
共同研究グループは、ポリイミド電着法[3]を用いてワイヤの表面に極薄のポリイミド絶縁皮膜を形成し、レアアース系の次世代高温超伝導ワイヤの絶縁部分の厚みを従来の10分の1以下にすることに成功しました。この方法は、数kmの長さのワイヤにも容易に適用できるため、これまでの絶縁材料のポリマーテープを巻いたワイヤよりも少ない工程で簡単に超伝導コイルを製作できます。また、開発したワイヤの断面積の絶縁比率は10%以下で、50%以上の従来のワイヤに比べてはるかに小さく、超伝導コイルの電流密度を2倍以上に大きく、体積を5分の1以下に小型化できます。
今回の成果は、高温超伝導を使った次世代の装置や機器の実用化に向け大きなインパクトになります。
本研究成果は、科学雑誌『Physica C』オンライン版に近日掲載されます。
背景
現在利用されている超伝導を応用した装置・機器は、冷却のために高価な液体ヘリウム(-272.20℃)を用いており、より安価な液体窒素(-195.8℃)や冷凍機による冷却で代替できる高温超伝導の実用化が求められています。高温超伝導材料のワイヤ化はビスマス系ワイヤが先行して開発されてきましたが、イットリウムなどのレアアース系ワイヤは高い電流密度と強靭な機械的強度を持ち、他の線材では達し得ない高磁場かつ小型の超伝導コイルを実現する次世代高温超伝導ワイヤとして注目されています(図1)。これまでに開発された同ワイヤは、幅が4~5mm、厚さが100~150μmと非常に薄い形状をしています。しかし、ワイヤにポリマーテープを巻きつけるこれまでの絶縁法では、絶縁部分の厚さが両側で100μm程度とワイヤと同じくらいの厚さとなり、絶縁部分がワイヤの断面のうち半分以上を占めてしまいます(図1)。この結果、超伝導コイルの断面あたりで流せる電流密度が小さくなり、十分な電流が流れる超伝導コイルを作るためには、大型化するしかありませんでした。もし、絶縁部分の厚さを1桁以上薄くできれば、高温超伝導コイルを大幅に小型化できるので、極薄の絶縁を作り出す技術の実現が待たれていました。しかし、ワイヤの角(かど)部では絶縁皮膜の厚さが不十分になりワイヤの表面が露出してしまうため、角部を持ったテープ形状のワイヤに、極薄の絶縁皮膜を均一な厚さで形成することは極めて困難とされてきました。
研究手法と成果
共同研究グループは、ポリイミド電着法と呼ばれる技術を用いてワイヤの表面全体に極薄かつ均一な厚みのポリイミド絶縁皮膜を形成することを試みました。この方法は、帯電させたポリイミドの粒子を、ワイヤの表面に固着させるもので、ワイヤの角部にも薄く均一な絶縁皮膜を形成することが可能です。この方法によりレアアース系の次世代高温超伝導ワイヤの絶縁部分の厚みを従来の10分の1以下の4μm(片側)にすることに成功しました(図2)。この絶縁被膜の生成法は、超伝導コイルを作るのに必要とされる数kmの長さのワイヤにも容易に施すことができます。また、これまでのポリマーテープを巻きつける方法に比べて、テープの切れや偏りの心配がないため、より簡単に超伝導コイルを製作できます。
この結果、開発したワイヤの断面積における絶縁部分の比率は10%以下となり、従来のワイヤが50%程度であったのに比べてはるかに小さくなりました。これにより、超伝導コイルの電流密度が従来より2倍程度大きくできるため、コイルが大幅に小型化できます。例として、内径が10cmで中心部に10テスラの磁場を発生させる超伝導コイルをレアアース系の次世代高温超伝導ワイヤで製作することを想定すると、今回開発した絶縁ワイヤ(絶縁部分の厚み4μm)の場合、従来の絶縁ワイヤ(絶縁部分の厚み50μm)の場合と比べ、必要な線材量が5分の1以下になると考えられます(図3)。
従来のレアアース系の次世代高温超伝導ワイヤを用いた超伝導コイルには、コイル製作時に生じる超伝導特性の劣化という課題もあります。同ワイヤは金属基板、中間層、超伝導層、銀層、銅安定化層からなる多層構造をしており(図1)、超伝導コイルの製作時では、コイルを巻いた後にエポキシ樹脂で含浸(がんしん)し、加熱して硬化させる手法(超伝導コイルのエポキシ含浸[4])をとります。本研究グループの先行研究(T.Takematsu et al, Physica C,470,2010,p.674-677.)から、レアアース系の次世代高温超伝導ワイヤのコイルをエポキシ樹脂で含浸して硬化させると、コイルの冷却時に多層構造が剥離しコイルの超伝導特性が大きく劣化することが分かっていました(図4a)。しかし、今回の方法で用いた絶縁部分のポリイミド皮膜には、ポリイミドの分子鎖にシロキサンという特別な構造を導入し、冷却による剥離を防止する機能を持たせています。これにより、エポキシ含浸・硬化の工程を経てもコイルの超伝導特性の劣化が生じないという、優れた特性があります(図4b)。
今後の期待
今回開発したポリイミド極薄絶縁を施したレアアース系次世代高温超伝導ワイヤは、コンパクトな高温超伝導コイル開発をするための基盤となる技術です。これまで実現できなかった超高磁場のNMRやMRI、超伝導リニアモーターにおける超伝導磁石の軽量化など、基礎科学、医療、工学分野における高温超伝導機器の実用化に向け大きな進展が期待できます。
原論文情報
- Y. Yanagisawa, K. Sato, T. Matsuda, T. Nagato, H. Kamibayashi, H. Nakagome, X. Jin, M. Takahashi, and H. Maeda.
"An ultra-thin polyimide insulation coating on REBCO conductors by electrodeposition produces a maximum overall current density for REBCO coils".
Physica C,2013,doi:10.1016/j.physc.2013.07.009
発表者
理化学研究所
ライフサイエンス技術基盤研究センター 構造・合成生物学部門 NMR施設
施設長 前田 秀明 (まえだ ひであき)
基礎科学特別研究員 柳澤 吉紀 (やなぎさわ よしのり)
お問い合わせ先
ライフサイエンス技術基盤研究センター
チーフ・サイエンスコミュニケーター 山岸 敦 (やまぎし あつし)
Tel: 078-304-7138 / Fax: 078-304-7112
報道担当
理化学研究所 広報室 報道担当
Tel: 048-467-9272 / Fax: 048-462-4715
補足説明
- 1.超伝導ワイヤ、次世代高温超伝導ワイヤ
超伝導材料を線材化したものを超伝導ワイヤと呼び、超伝導コイルなどに用いられる。現在実用化されている超伝導ワイヤは希少で効果な液体ヘリウム(-272.20℃)による冷却を必要とするのに対し、液体窒素(-195.8℃)や冷凍機による冷却で代替できる高温超伝導の性質を備えた線材の開発が試みられている。高温超伝導ワイヤの開発はビスマス元素を用いたものが先行しており、これに対してイットリウム等の希土類(レアアース)元素を使用するものを次世代高温超伝導ワイヤと呼ぶ。 - 2.電流密度
コイル断面の単位面積あたりに流せる電流値。これが大きいとコイルをコンパクトにできる。 - 3.ポリイミド電着法
正に帯電させたポリイミドの粒子を、負に帯電させたワイヤに固着させる手法。金属メッキと同じ原理。 - 4.超伝導コイルのエポキシ含浸
超伝導コイルのワイヤ間にエポキシ樹脂を浸透させ、これを熱処理によって硬化させることでワイヤ同士を接着させて一体化し、コイルに剛性を持たせる方法。従来の超伝導コイルの製作過程で、幅広く用いられてきた方法。
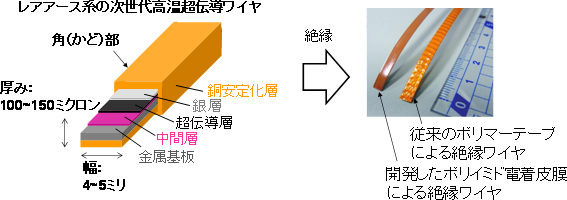
図1 レアアース系の次世代高温超伝導ワイヤ
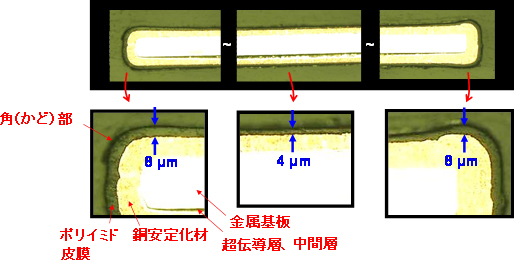
図2 ポリイミド電着法で絶縁した次世代高温超伝導ワイヤの断面写真
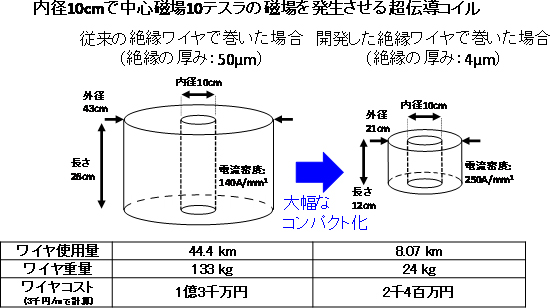
図3 今回開発した次世代高温超伝導ワイヤを用いたコイルの想定
従来の絶縁を施した次世代高温超伝導ワイヤと今回開発した極薄絶縁を施した次世代高温超伝導ワイヤを用いて、それぞれ10テスラの磁場を発生させるコイルの設計した場合のワイヤ使用量、ワイヤ重量、ワイヤコストの差。従来に比べて大幅なコストダウンが可能。
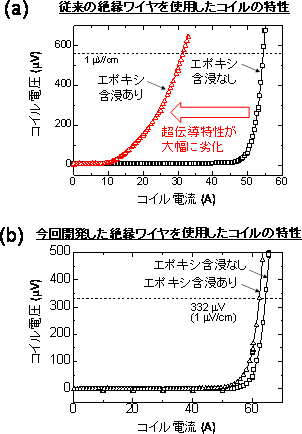
図4 従来の絶縁を施した次世代高温超伝導ワイヤ(a)と今回開発した(b)極薄絶縁を施した次世代高温超伝導ワイヤを使ったコイルの特性
- (a) コイルの冷却時に多層構造が剥離しコイルの超伝導特性が大きく劣化する。
- (b) 絶縁部分のポリイミド皮膜に、ポリイミドの分子鎖にシロキサンという特別な構造を導入し、冷却による剥離を防止する機能を持たせた。これにより、エポキシ含浸・硬化の工程を経てもコイルの超伝導特性の劣化が生じない。