脱炭素に向けて、水素エネルギーを利用する計画が着々と進んでいます。水素社会の実現には、水素の貯蔵材料の開発が重要な鍵になります。理研と産業界が一体となって連携するバトンゾーン研究推進プログラムでは、従来の高性能活性炭の2倍量の水素を吸着できる材料を発見。水素の貯蔵材料の開発へと大きく前進しました。
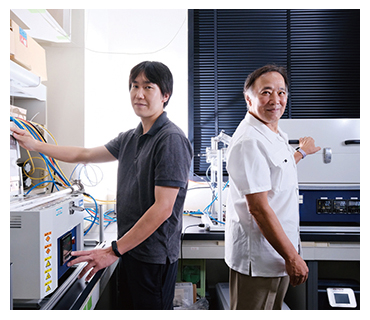
科技ハブ産連本部 バトンゾーン研究推進プログラム 水素エネルギーストレージ技術研究チーム
(右)内山 直樹(ウチヤマ・ナオキ)チームリーダー
(左)宮島 大吾(ミヤジマ・ダイゴ)副チームリーダー
水素の利用に不可欠な「貯蔵」の技術
2050年までに温室効果ガスの排出を実質的にゼロにすることを目指すカーボンニュートラルに向けて経済産業省が策定した「グリーン成長戦略」。その中で、水素は成長が期待される14の重点分野の一つに挙げられている。利用時に二酸化炭素を排出しない水素をエネルギーとして利用するには、さまざまな技術開発が必要だ。気体の水素を利用するには、水素をつくる、運ぶ、使用する、どの段階でもいかに効率よく水素を貯蔵できるかが鍵を握る。それには「圧縮」「吸蔵」「吸着」の方法があり、チームが取り組むのは、水素吸着材料だ。
「水素吸着材料」の競争と共創
内山 直樹 チームリーダーは、理研での研究を始める前から、株式会社アツミテックで水素吸着材料を東北大学と共同で研究開発してきた。ゼオライトという小さな穴の空いた材料を鋳型にして炭素材料を流し込み、焼成してゼオライトを除去する。すると、ゼオライト鋳型炭素(ZTC)という複雑な形状をした表面積の大きな炭素材料ができる(図1)。この表面積の大きさが水素をよく吸着する秘密だ。
一方で、宮島 大吾 副チームリーダーは、繰り返し構造を持つ高分子を合成する研究をしてきた。しかも、思い描いたとおりの欠陥構造を組み込むノウハウも持っていた。この二人がタッグを組んだのが水素エネルギーストレージ技術研究チームだ。
チームは、ゼオライトに代わる安価で合成の容易な多孔性材料である「理研MOF」の開発に着手した(MOFはMetal-Organic Frameworkの略で金属-有機構造体の意)。このMOFをさらに焼成して炭化し、欠陥構造を多数導入した「理研MOF炭化物」をつくり上げた(図2・図3)。注目すべきは、比表面積が小さくても欠陥構造で効率よく水素が吸着できる点だ。
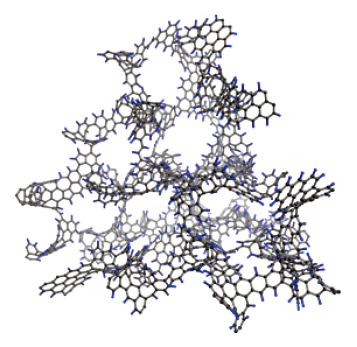
図1 ZTC
画像提供:東北大学材料科学高等研究所 西原 洋知 教授
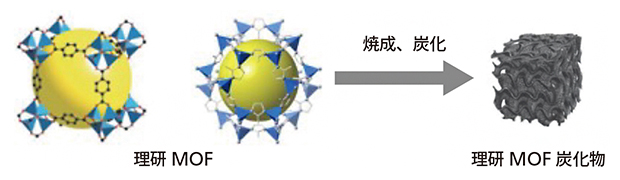
図2 理研MOF炭化物の生成法
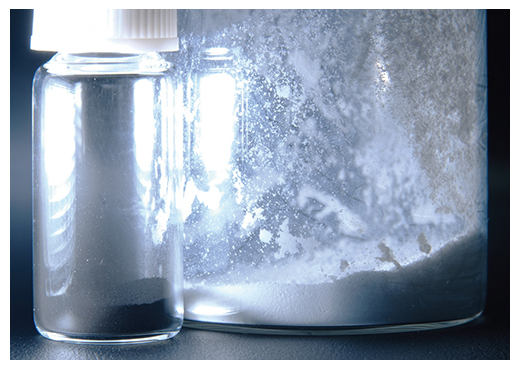
図3 焼成前の理研MOF(右)と焼成後に粉砕した理研MOF炭化物(左)
数百のサンプルを合成して検討を重ね、理研MOF炭化物は、従来の水素吸着材料(高性能活性炭)の約2倍の吸着能を達成した(図4)。気体を吸着する物質の性能はそれまで窒素の吸着能で示され比較されてきた。「窒素吸着能が高い物質が必ずしも水素吸着能が高いとは限りませんでした。これほど高い圧力まで水素吸着量を測定した研究はありません。今、水素吸着材料の研究領域を理研が牽引しているのです」(内山 チームリーダー)
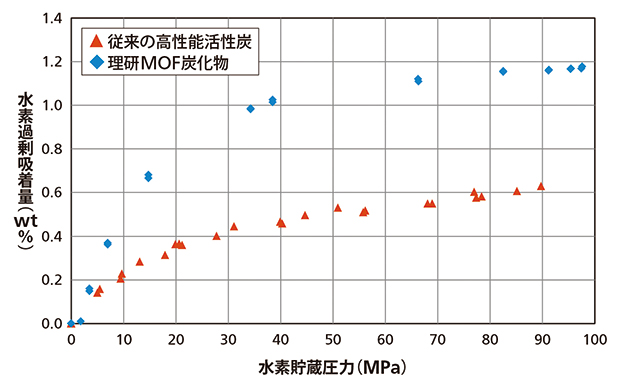
図4 従来の約2倍の吸着能を達成した理研MOF炭化物
グラフ右上にいくほど高圧下での吸着能の高さを示す。燃料電池車など、日本国内では70MPaの高圧水素貯蔵タンクが普及しているため、70MPa近傍の高圧域での性能評価も必要。
研究はどのように進められたのか、内山 チームリーダーはこう語る。「当初は、お互いが開発した材料の優れた点を目標値として設定し、競い合いながらそれぞれ改良を進めていきました。理研MOF炭化物は原料の入手しやすさや原価、製造コスト、製造安定性、安全性など実用化を見据えたときにZTCより優れていました」。宮島 副チームリーダーは「炭化が材料を強固にするという知見とその手法、どのような要素が品質に影響を与えやすいかなど、内山さんから詳細なノウハウを共有していただきました。超高圧での水素吸着能の評価法もアツミテックではすでに確立されていましたし、装置も使わせていただきました。理研だけで研究をしていたら、これほど速く成果を出せなかったでしょう」。
突然の出来事「性能が出ない」
ある日、それまでと同じように実験していたのに、なぜか理研MOF炭化物の水素吸着能が落ちてしまった。何度つくり直しても以前の性能は出ない。調べていくと、焼成の工程で品質が落ちていた。焼成する際に、理研MOF炭化物は窒素を充満したガラス管(プロフィール写真左装置中央)の中で加熱される。一番に窒素の品質を疑ったが、各社から窒素ボンベを取り寄せ試しても改善しなかった。材料合成に使う試薬も同様に確かめたが改善しない。結局、原因はガラス管の外側の空気の湿度だと判明した。実験室の冷暖房システムは季節によって切り替わる。その際、除湿のシステムも切り替わっており、室内の空気の湿度が高くなっていた。湿度がガラス管の温まり方を変えてしまい、焼成に悪影響を及ぼしていたのだ。ガラス管の外側、理研MOF炭化物には直接触れない空気の湿度を制御することで、かつての高い水素吸着能を再現できた。
"バトンゾーン"を存分に生かした研究推進
こうして粘り強く問題解決にあたる宮島 副チームリーダーについて内山 チームリーダーは「実験結果について理論的な考察をし、納得がいくまで研究する。一方で、たった一回良いデータを記録すればよいといった興味、関心よりも、コストや再現性、安全性といった実用化のために不可欠な条件を基礎研究の段階から考慮に入れて研究する姿勢に感服した」と言う。
一方、宮島 副チームリーダーの方も、「求めた品質ではない材料でも、活用できる別用途を思いついたり、別の物質を混ぜて品質を補うなどのアイデアが次々と出てくるんです。材料を研究すると単独で優れた材料ばかりに目がいって、ついつい視野が狭くなってしまいがち。柔軟な解決法は自分ではなかなか思いつけません。内山さんはチーム全体を統括する立場ですが、実験の詳細まで熟知した上で一緒に考えてくれます」と信頼を寄せる。
互いの強みを生かし、数多くのディスカッションを重ねて、優れた水素吸着能を持つ材料を見出したバトンゾーンで、スケールアップに向けた研究も始まっている。「『あの燃料電池車に私が研究した技術が入っている』と知人に話せるような研究を続けたいですね」と、二人は目を輝かせる。
(取材・構成:大石かおり/撮影:相澤正。/制作協力:サイテック・コミュニケーションズ)
この記事の評価を5段階でご回答ください